Évitez les arrêts avec une nouvelle technologie de détection des fuites d'hydrogène
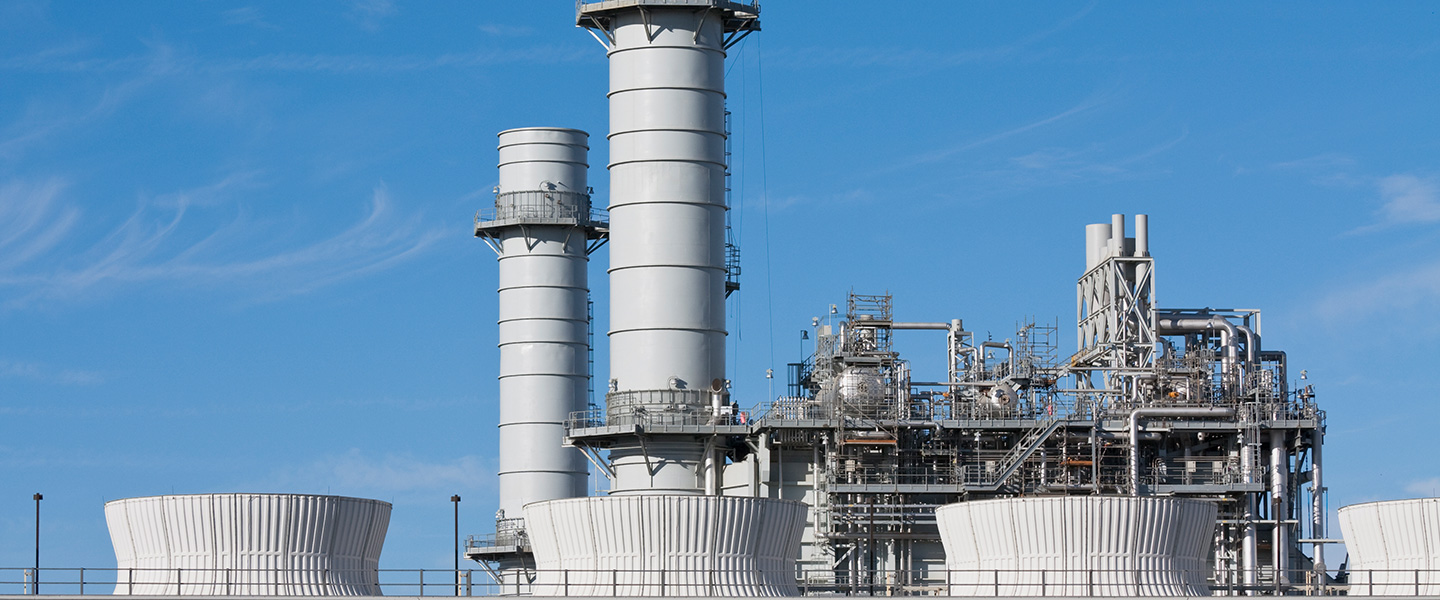
La maintenance des générateurs refroidis à l'hydrogène est essentielle pour la sécurité et le bon fonctionnement d'une centrale électrique. La détection et la réparation des fuites d'hydrogène du système de refroidissement peuvent nécessiter d'importantes recherches au niveau des composants, des valves, des raccords ou autres éléments du système. Les méthodes classiques de détection des fuites d'hydrogène ont tendance à être plus efficaces pour identifier la présence d'hydrogène dans de vastes zones que pour repérer l'origine de la fuite. L'arrivée des caméras d'imagerie optique du gaz a rendu la détection des fuites beaucoup plus efficace et performante. Avec l'ajout d'une caméra infrarouge dédiée pour la détection des fuites de CO2, les compagnies disposent désormais d'un moyen efficace pour détecter les fuites d'hydrogène en utilisant le CO2 comme gaz traceur.
Le fonctionnement d'un générateur électrique produit une grande quantité de chaleur qui doit être éliminée pour préserver l'efficacité de l'équipement. Selon les capacités nominales du générateur, il sera refroidi à l'air, à l'hydrogène, à l'eau voire, pour les plus volumineux, par une combinaison d'eau pour le stator et d'hydrogène pour le rotor. Le refroidissement à l'hydrogène offre un excellent rendement grâce à sa faible densité, sa chaleur spécifique élevée et sa conductivité thermique. Cependant, l'hydrogène est hautement combustible lorsqu'il est mélangé à l'air, et il peut être dangereux si sa concentration augmente dans une zone indésirable. Les générateurs à turbine évacuent de l'hydrogène dans le cadre de leur fonctionnement normal et s'appuient sur une ventilation adéquate pour éviter que les concentrations d'hydrogène ne posent un risque d'explosion. La sécurité de l'hydrogène est donc cruciale pour les opérateurs de centrales.
Les molécules d'hydrogène sont très légères et petites, et donc difficile à contenir. Entre les pannes, l'usure des vannes, des joints et de l'équipement peut permettre la formation de fuites importantes et l'accumulation de concentrations d'hydrogène dans des zones dangereuses pour la sécurité de l'usine. La quantité d'hydrogène ajoutée chaque jour est surveillée avec le plus grand soin. Toute augmentation de ce complément doit faire l'objet d'une enquête car il indique une fuite. Les méthodes traditionnelles de détection et correction des fuites (LDAR) sont généralement lentes et n'identifient pas la fuite assez vite pour éviter l'arrêt. Une période d'arrêt peut durer de deux à trois semaines, la détection de la fuite occupant à elle seule plusieurs journées de travail. Les coûts associés à un arrêt non planifié peuvent atteindre plusieurs millions de dollars pour une compagnie d'électricité. L'industrie préférerait effectuer les activités de détection et correction des fuites (LDAR) en ligne pour éviter les coupures imprévues, mais elle subissait jusqu'ici les limitations des méthodes de découverte de la source.
Méthodes de détection traditionnelles
Les méthodes de détection des fuites sont variées. On peut utiliser une solution d'eau savonneuse pour faire apparaître des bulles sur chaque composant candidat, ou utiliser des capteurs d'hydrogène microélectroniques (renifleurs) pour détecter l'hydrogène sur une zone plus vaste. L'eau savonneuse suffit pour contrôler un seul composant, mais rechercher une fuite dans un lieu inconnu pourrait prendre des semaines. De plus, cette méthode ne fonctionne que pour les fuites minimes car un débit d'hydrogène trop important peut repousser la solution sans former de bulles. Le renifleur est une sonde manuelle qui produit un signal sonore à proximité d'une fuite. Si cette méthode de détection est relativement abordable, elle présente certains inconvénients. Les générateurs sont bien ventilés. Cela peut diluer l'hydrogène, à moins de se trouver à grande proximité de la source. La ventilation peut également déplacer l'hydrogène à grande distance de la source et ainsi déclencher des faux positifs sans pour autant localiser le composant nécessitant des réparations. Les renifleurs ne permettent pas non plus à l'opérateur de voir la fuite. Cette méthode implique toujours des approximations et des pertes de temps dans la recherche de la source d'une fuite.
Une nouvelle approche
Évolution récente de la technologie de détection de gaz, les caméras infrarouges gagnent en popularité auprès des équipes de maintenance. Les caméras infrarouges, ou à imagerie thermique, sont utilisées avec succès pour détecter les défauts d'isolation dans les bâtiments ou localiser les risques de sécurité associés à la chaleur dans les installations électriques. L'imagerie optique des gaz, associée à une caméra thermique, est apparue il y a quelques années, utilisant le SF6 comme gaz traceur. Toutefois, certaines compagnies s'inquiètent de l'utilisation du SF6, en raison de son coût, de son potentiel de réchauffement global (PRG 23 000) et, dans certains cas, des restrictions imposées sur l'utilisation du SF6. FLIR Systems s'est associé à l'industrie pour mettre au point une nouvelle génération d'imageurs optiques des gaz utilisant un traceur capable de répondre à ces inquiétudes. La nouvelle caméra d'imagerie optique des gaz FLIR GF343 utilise comme gaz traceur le CO2, un gaz immédiatement disponible dans les centrales électriques. Le CO2 est peu coûteux, il présente un PRG très inférieur et son utilisation est beaucoup moins restreinte que celle du SF6. Cette nouveauté élargit considérablement l'éventail des cas d'utilisation de l'OGI pour la détection des fuites. Comme il suffit d'ajouter une faible concentration de CO2 (généralement 3 à 5 %) comme gaz traceur à l'hydrogène pour rendre les fuites visibles par la caméra OGI, le niveau de pureté de l'hydrogène dans la turbine est préservé et les opérations normales de génération peuvent se poursuivre. Avec la FLIR GF343, les techniciens disposent d'un nouvel outil pour localiser la source des fuites sans arrêter la centrale.
Détection du CO2 traceur
Du fait de l'ajout d'une faible concentration de CO2 (< 5 %) comme gaz traceur à l'alimentation en hydrogène, le générateur peut continuer de fonctionner à un niveau sûr et efficace. Les équipes d'opérations et de maintenance peuvent ainsi surveiller et rechercher les fuites d'hydrogène pendant le fonctionnement du générateur. Lors de tests effectués aux États-Unis et en Italie, il a été démontré que la FLIR GF343 peut visualiser une petite quantité (~2,5 %) de CO2 comme gaz traceur dans le système en cas de fuite, permettant ainsi aux équipes de maintenance de localiser les fuites avec précision et de les signaler pour la prochaine intervention de maintenance planifiée ou, dans le cas d'une fuite plus importante, pour réparation immédiate. Grand avantage de la GF343 par rapport aux autres technologies de détection, la détection des fuites peut désormais se faire pendant le fonctionnement de l'équipement, ce qui fait gagner du temps et de l'argent en réduisant les temps d'arrêt. Les arrêts peuvent être réduits de deux, voire trois jours, et quand on sait que chaque jour d'arrêt coûte entre 80 000 et 100 000 $ (selon le type et la taille du générateur), le retour sur investissement de l'utilisation du CO2 comme gaz traceur avec la caméra FLIR GF343 s'avère considérable. Mais les petites fuites n'ont pas le seul défaut d'être très fréquentes : elles peuvent aussi se transformer en grosses fuites. Avec la FLIR GF343, les équipes de maintenance peuvent conserver à temps la concentration d'hydrogène atmosphérique en dessous du seuil d'explosion.
Fonctionnement de la FLIR GF343
La FLIR GF343 utiliser un détecteur en antimoniure d’indium (InSb) à matrice à plan focal (MPF) offrant une réponse de détection comprise entre 3 et 5 μm, laquelle est ensuite spectralement adaptée à environ 4,3 μm à l'aide d'un filtre refroidi et du refroidissement du détecteur par un moteur sterling à des températures cryogéniques (autour de 70 °K soit -203 °C). La technique d'ajustement spectral ou de filtre refroidi est cruciale pour la technique d'imagerie optique des gaz et, dans le cas de la FLIR GF343, elle rend la caméra particulièrement réactive et ultra-sensible à l'absorption infrarouge du CO2.
Concrètement, l'énergie de l'arrière-plan provenant notamment du ciel, du sol ou d'autres sources présentes dans le champ de vision de la caméra, est absorbée par le gaz. La caméra met cette absorption d'énergie en évidence au moyen d'un contraste thermique dans l'image. La caméra ne montre pas seulement l'absorption spectrale, mais aussi le mouvement du gaz, vous permettant de le visualiser sous la forme d'une volute de « fumée ».
La GF343 comprend également une technique de soustraction d'image qui renforce la visibilité du mouvement du gaz. Le mode haute sensibilité (HSM) est la pierre angulaire de la détection des fuites les plus ténues. Le HSM est en partie une technique de traitement vidéo par soustraction d'images qui améliore effectivement la sensibilité thermique de la caméra. Un pourcentage des signaux de pixel présents dans les images du flux vidéo est soustrait des images suivantes, ce qui rend le mouvement des gaz plus visibles et améliore concrètement la sensibilité globale de la caméra, et donc sa capacité à localiser les plus petites fuites de CO2, même sans utiliser de trépied.