Contrôle qualité intégral des résistances avec une caméra thermique FLIR
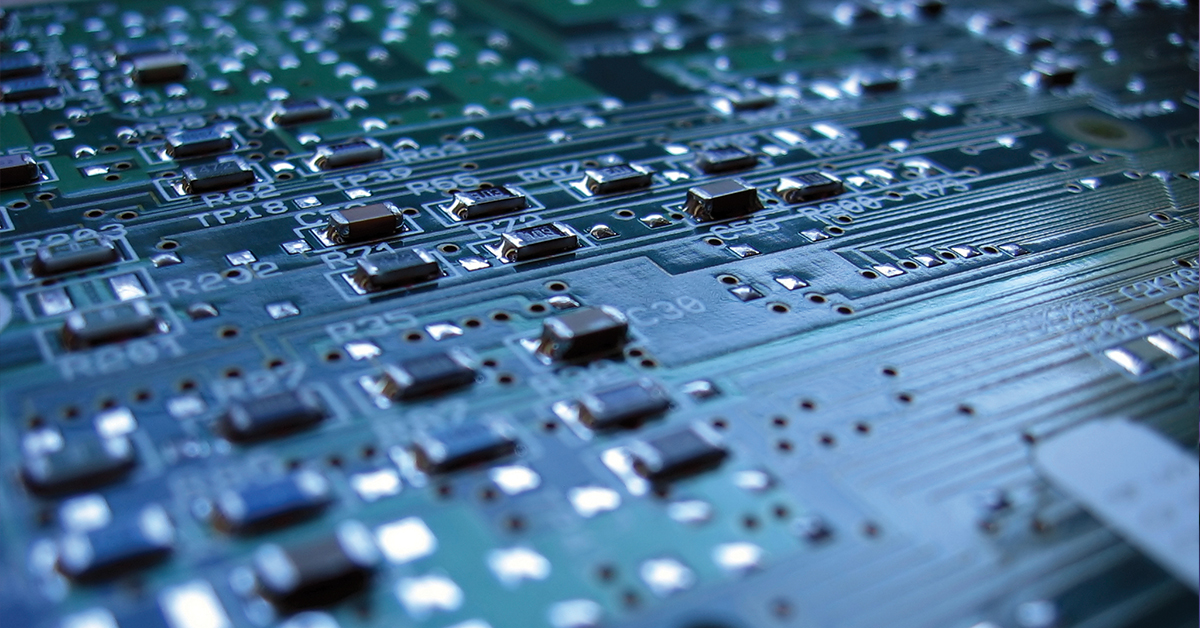
Il est essentiel de réduire le taux de défaillance des composants électroniques dans les entreprises voulant proposer un produit d'excellente qualité à leurs clients. La seule façon d'y parvenir est de vérifier chaque composant afin de fournir un contrôle qualité intégral. Isabellenhütte, un fabricant d'alliages résistants pour les thermocouples, d'alliages pour les rallonges et de composants passifs utilisés dans le secteur automobile, a répondu à cette exigence à l'aide d'une caméra thermique FLIR Systems.
Ce fabricant est situé à Dillenburg, près de Francfort, en Allemagne. Les produits de Isabellenhütte sont utilisés par le secteur automobile dans les moteurs à injection diesel ainsi que dans d'autres boîtiers électroniques. L'entreprise jouit d'une réputation internationale bien méritée pour la qualité élevée de ses produits. Afin d'atteindre et de conserver les niveaux de qualité élevés demandés par ses clients du monde entier, l'entreprise investit massivement dans le contrôle qualité ainsi que dans la recherche et le développement.
Réduction des taux de défaillance par un contrôle intégral
Malgré ces investissements, les clients continuaient de signaler des taux de défaillance de l'ordre de 5 p.p.m. Selon les normes en vigueur chez Isabellenhütte, même un taux de défaillance de 10-8 était inacceptable. L'entreprise a alors décidé de mettre en place un contrôle intégral de tous les composants. Les points faibles des composants peuvent apparaître durant le processus de fabrication et ces derniers peuvent ensuite occasionner des défaillances dans les produits électroniques intégrés. En conséquence, les systèmes électroniques finaux ne présenteront pas la durabilité souhaitée, ce qui entraînera d'éventuels problèmes de qualité, tant pour le fournisseur de l'appareil que pour le constructeur automobile.
La solution adoptée par Isabellenhütte a été d'installer une caméra thermique FLIR Systems. Cette dernière sert à inspecter chaque composant fabriqué. En moins d'une seconde, le système réalise une image infrarouge qui permet de vérifier la présence d'éventuels défauts sur la résistance. Ces derniers apparaissent sous forme de points chauds dans l'image, et résultent de la hausse de température à la surface d'un appareil défaillant.
Durant le processus de contrôle qualité, chaque résistance est chargée durant un laps de temps très court. En l'espace de 20 ms, la caméra thermique observe le cycle thermique du composant. Utilisation du logiciel de traitement d'image IRCheck conçu par l'intégrateur système
Technologie d'automatisation
(www.automationtechnology.de), l'ordinateur compare la température maximum détectée avec la température de surface moyenne de la résistance. Si la différence entre les valeurs maximum et moyenne excède une valeur prédéfinie, ceci signifie que le composant présente un point chaud. Lorsqu'un point chaud est détecté, un signal de déclenchement est automatiquement émis pour retirer le composant défaillant de la ligne de production. L'ensemble du processus dure moins d'une seconde, de l'entrée à la sortie de la machine de test. L'image thermique présentant la zone défectueuse du composant est enregistrée dans une base de données à des fins statistiques de contrôle du processus.
Des normes de qualité encore plus élevées
« La thermographie infrarouge, et en particulier la caméra thermique FLIR Systems, s'est révélée un moyen parfait de garantir des normes de qualité encore plus élevées qu'avant », déclare M. Eichman, chef de production chez Isabellenhütte. « Nous contrôlons désormais notre production 24/24 heures. Étant donné que nous n'avons plus besoin d'opérateur pour le faire, nous réalisons des économies. Notre investissement initial dans la caméra thermique a été amorti en un temps très court. Plus important encore, chacune des résistances est désormais contrôlée, ce qui nous permet de fournir un produit parfait à nos clients ».
Il va sans dire que les efforts déployés par Isabellenhütte pour fournir un produit parfait sont extrêmement appréciés par sa clientèle exigeante, et lui permettent de conserver
un positionnement de leader dans le secteur.
Principe du contrôle qualité infrarouge :
- Chaque résistance est chargée électriquement durant un laps de temps très court.
- Un instantané de 20 ms est réalisé avec la caméra thermique FLIR Systems
- La différence entre les température de surface maximum et moyenne du composant est comparée à une valeur prédéfinie.
- En cas de détection d'un composant défaillant, un signal de déclenchement est automatiquement émis pour retirer le composant de la ligne de production.
- L'image thermique correspondante est enregistrée dans une base de données à des fins statistiques de contrôle de la qualité.
Configuration du système :
- Une caméra thermique FLIR avec une interface numérique à grande vitesse et une fréquence d'acquisition de 50 images/s
- Un objectif macro 34/80 avec un champ de vision horizontal de 34 mm et une distance focale de 80 mm
- Des composants industriels comme des câbles blindés, un rack 19" et un ordinateur exécutant Windows® NT™
Principaux avantages pour le client :
- Contrôle qualité entièrement automatisé
- Fonctionnement 24/24 h sans recours à un opérateur
- Contrôle qualité à 100 % de chaque composant
- Réduit considérablement le taux de défaillances ultérieures du système
FLIR A310
La caméra thermique utilisée pour cette application est la ThermoVisionTM A320M. Ce modèle a été remplacé par la FLIR A310, un modèle encore plus performant
La FLIR A310 est une caméra compacte à montage fixe qui peut être installée quasiment partout. Elle peut mesurer les différences de température de l’ordre de seulement 0,05 ºC. La fonction d'analyse exclusive des mesures et les fonctions d'alarme font de la FLIR A310 un outil parfait pour de nombreuses applications.